
5 common myths about linerless labels and why they’re untrue
Linerless labels are becoming an increasingly popular choice in industries such as retail, logistics, and food service due to their efficiency and environmental benefits. Unlike traditional labels, they do not have a backing liner, reducing waste and maximizing roll capacity. However, despite their advantages, several misconceptions persist, preventing some businesses from fully adopting this innovative solution.
These myths often arise from outdated information or misunderstandings about how linerless labels function in modern applications. Some businesses believe that linerless labels are less reliable, more expensive, or difficult to use, while others question their durability and sustainability. In reality, advancements in adhesive technology and thermal printing have significantly improved their performance, making them as effective—if not more—than traditional labels.
In this article, we will debunk the most common myths about linerless labels and explain why they are untrue. By understanding the facts, businesses can make informed decisions, improve their cost-efficiency, and contribute to a more sustainable approach to labeling.
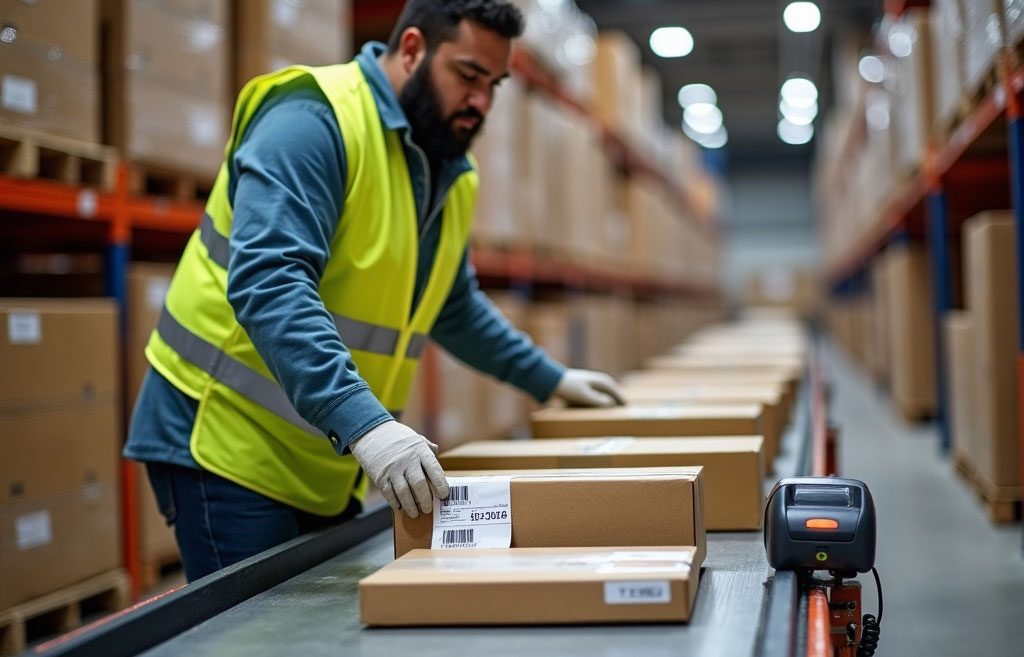
Myth 1: Linerless labels are less reliable than traditional labels
One of the most persistent misconceptions about linerless labels is that they do not adhere as well as traditional labels and may fail in demanding conditions. Many businesses worry that without a liner, the labels might be difficult to apply or could lose their adhesive properties over time.
Advanced adhesive technology ensures strong and lasting adhesion
In reality, linerless labels use advanced adhesive technology that ensures strong adhesion on a wide variety of surfaces, including packaging materials, plastic, and even slightly textured surfaces. Unlike traditional labels that rely on a release liner to protect the adhesive until use, linerless labels are coated with a special silicone layer, preventing sticking until pressure is applied during application. This means they perform just as reliably as traditional labels, if not better.
Additionally, linerless labels have been extensively tested in industries where durability is critical. In logistics and shipping, they withstand temperature changes, humidity, and rough handling without peeling or fading. In food service, they adhere to various packaging materials while complying with food safety regulations.
Another key advantage is that linerless labels offer a more consistent application process, reducing the risk of label curling or misalignment. Many automated label dispensers are designed specifically for linerless labels, ensuring smooth and precise application in high-speed production environments.
By eliminating unnecessary waste and offering equal or superior performance, linerless labels are proving to be a reliable and efficient alternative to traditional labels.
Myth 2: Linerless label printers are expensive and hard to maintain
Another common myth is that businesses need to invest in costly specialized printers for linerless labels and that these printers require frequent maintenance. This misconception often discourages companies from exploring linerless technology, despite its long-term benefits.
Long-term savings outweigh initial investment and reduce maintenance needs
While linerless label printers may have a slightly higher upfront cost, they offer significant savings over time. Traditional labels with liners create excess waste, requiring businesses to spend more on disposal and waste management. Linerless labels eliminate this issue, maximizing roll capacity and reducing the frequency of roll changes. This means fewer production interruptions and lower material costs.
Additionally, modern linerless printers, such as APS thermal printers, are designed for efficiency and durability. They feature advanced cutting mechanisms that precisely cut labels to the required length, reducing unnecessary label usage.
Maintenance concerns are often exaggerated. Since linerless labels produce no liner waste, printers experience less paper buildup and debris accumulation, leading to fewer mechanical issues over time. Many companies that switch to linerless label printing find that maintenance costs decrease due to the reduced need for frequent cleaning and component replacements.
When considering the total cost of ownership, linerless label printers provide a more sustainable and economical solution. The combination of reduced waste, lower material costs, and fewer maintenance requirements makes them a smart investment for businesses looking to optimize their labeling operations.
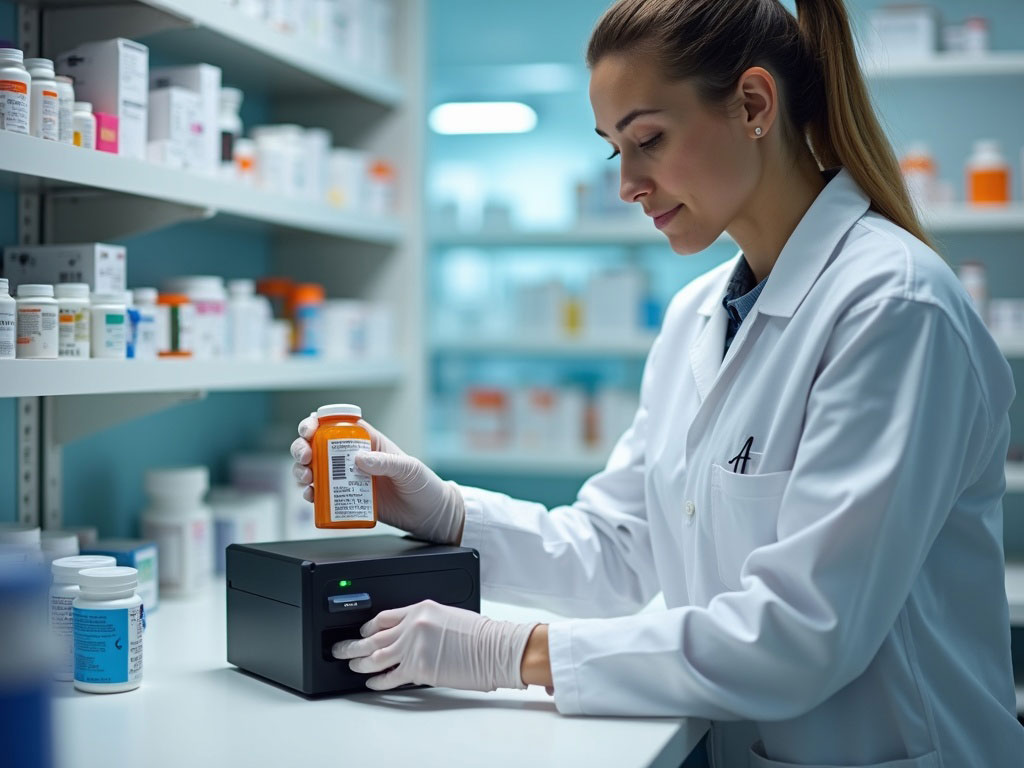
Myth 3: Linerless labels limit design and customization
A widespread belief is that linerless labels offer fewer design and customization options compared to traditional labels. Some assume that they are only available in standard sizes and cannot accommodate branding, barcodes, or other variable data.
Variable-length printing offers more flexibility than traditional labels
In reality, linerless labels provide more flexibility than traditional labels. Unlike pre-cut labels, linerless labels are printed and cut at variable lengths, allowing businesses to customize each label according to their specific needs. This eliminates the constraint of fixed label sizes and enables companies to print only what is required, reducing material waste.
Linerless labels are also compatible with high-resolution thermal printing, ensuring that logos, barcodes, QR codes, and detailed product information are clear and sharp. Modern printing technology supports multiple colors and different adhesive strengths, making linerless labels suitable for a wide range of applications, from retail shelf labeling to logistics tracking.
Another important advantage is their adaptability to different industries. In food service, linerless labels can be used for ingredient lists and expiration dates, adjusting to different package sizes with a single roll. In healthcare, they allow for precise patient identification and compliance with strict labeling regulations.
Moreover, linerless label printing systems can integrate with existing labeling software, enabling businesses to create custom templates and automate label generation without the need for expensive proprietary software.
The idea that linerless labels are limited in design is outdated. In reality, they offer businesses greater flexibility, efficiency, and customization opportunities, while reducing material usage and environmental impact.
Myth 4: Linerless labels are not environmentally friendly
Some businesses assume that linerless labels are not a truly sustainable solution, believing that they still generate waste or require more resources to produce. This misconception arises from the fact that linerless labels contain adhesive coatings, leading some to question their environmental impact.
Reducing waste and improving sustainability
In reality, linerless labels are significantly more eco-friendly than traditional labels. One of their biggest advantages is the elimination of the liner, which reduces paper waste by up to 40-50% per roll. This means fewer raw materials used in production and less waste to dispose of after use. Since liner waste cannot be easily recycled due to its silicone coating, switching to linerless labels helps businesses cut down on landfill waste and reduce their overall carbon footprint.
Linerless labels also contribute to lower transportation and storage costs. Because they contain more labels per roll, they require less space, reducing fuel consumption during shipping. This results in fewer deliveries, lower CO₂ emissions, and a more sustainable supply chain.
Additionally, many linerless label materials are now made from recyclable or responsibly sourced paper, further minimizing their environmental impact. By adopting linerless labels, businesses can align with corporate sustainability goals while also benefiting from cost-efficient labeling solutions.
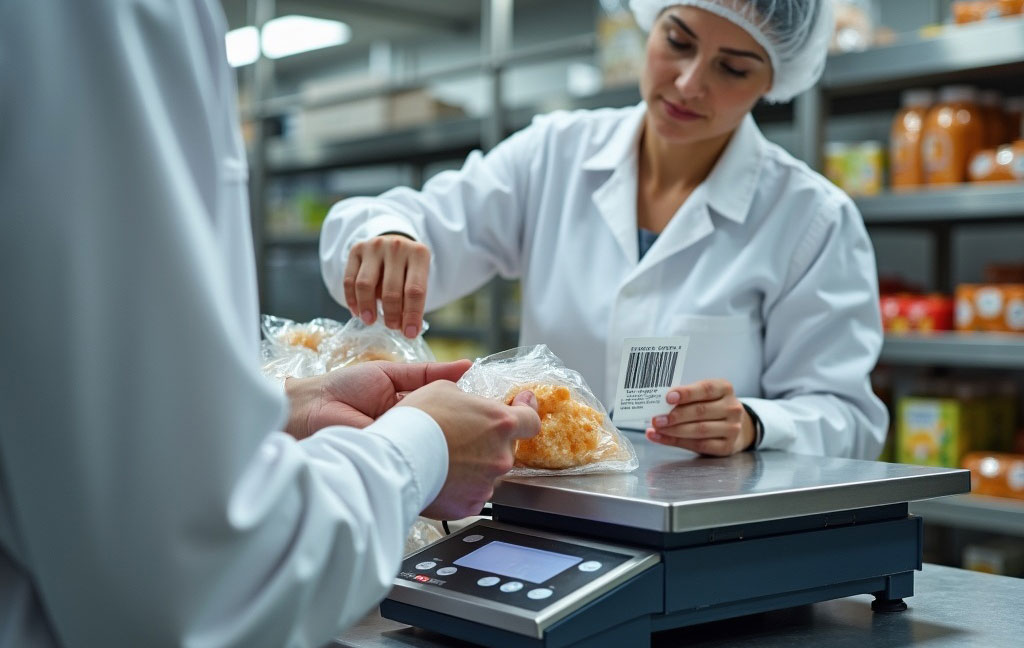
Myth 5: Linerless labels are difficult to apply and handle
A common concern among businesses is that linerless labels are harder to dispense, apply, or handle without the support of a liner. Some assume that the adhesive might make them stick together or cause issues during high-speed application.
Optimized for smooth application, both manually and automatically
However, linerless labels are designed with a special silicone coating that prevents them from sticking to themselves before application. This allows for smooth and controlled dispensing, whether applied manually or through automated systems. Modern linerless label printers are equipped with precision cutting mechanisms, ensuring each label is cleanly cut and ready for use without the need for a liner.
For businesses using high-speed labeling systems, linerless labels integrate seamlessly with automated dispensing equipment. The lack of a liner reduces the risk of jams, improves application accuracy, and eliminates the downtime caused by manually removing and disposing of liners. In industries like food service and logistics, where fast labeling is essential, linerless labels provide an efficient solution that keeps operations running smoothly.
Even in manual labeling environments, linerless labels are easy to handle. Many businesses report that employees prefer linerless rolls because they eliminate the hassle of dealing with liner waste, making the process cleaner and more efficient.
By adopting linerless labels, businesses can benefit from faster, more efficient application, whether through automation or manual use, without compromising accuracy or usability.
APS linerless thermal printers: efficiency, reliability, and sustainability
If you’re considering switching to linerless labels, choosing the right printing technology is essential. APS offers a range of high-performance linerless thermal printers designed to deliver precision, reliability, and cost savings across various industries.
Designed for high-efficiency labeling
APS linerless thermal printers are built to handle continuous, high-speed printing without compromising quality. With advanced cutting mechanisms, they allow businesses to print labels at variable lengths, optimizing material use and reducing waste. The precision-cutting system ensures that each label is neatly dispensed, improving workflow efficiency.
Lower operational costs and reduced maintenance
One of the biggest advantages of APS linerless printers is their cost efficiency. By eliminating liners, businesses can fit more labels per roll, reducing frequent roll changes and minimizing downtime. Additionally, fewer moving parts and an optimized paper path lead to lower maintenance needs, making APS printers a smart long-term investment.
Seamless integration into any industry
Whether for retail, logistics, food service, healthcare, or ticketing, APS linerless printers provide versatile labeling solutions. Designed for easy integration with existing systems, they support various connectivity options and industry-standard software, ensuring a smooth transition for businesses looking to upgrade their labeling operations.
A sustainable choice for forward-thinking businesses
APS linerless printers help businesses meet sustainability goals by reducing waste, shipping volume, and overall material consumption. With a focus on eco-friendly innovation, APS continues to develop high-quality, energy-efficient printing solutions that contribute to a more sustainable supply chain.
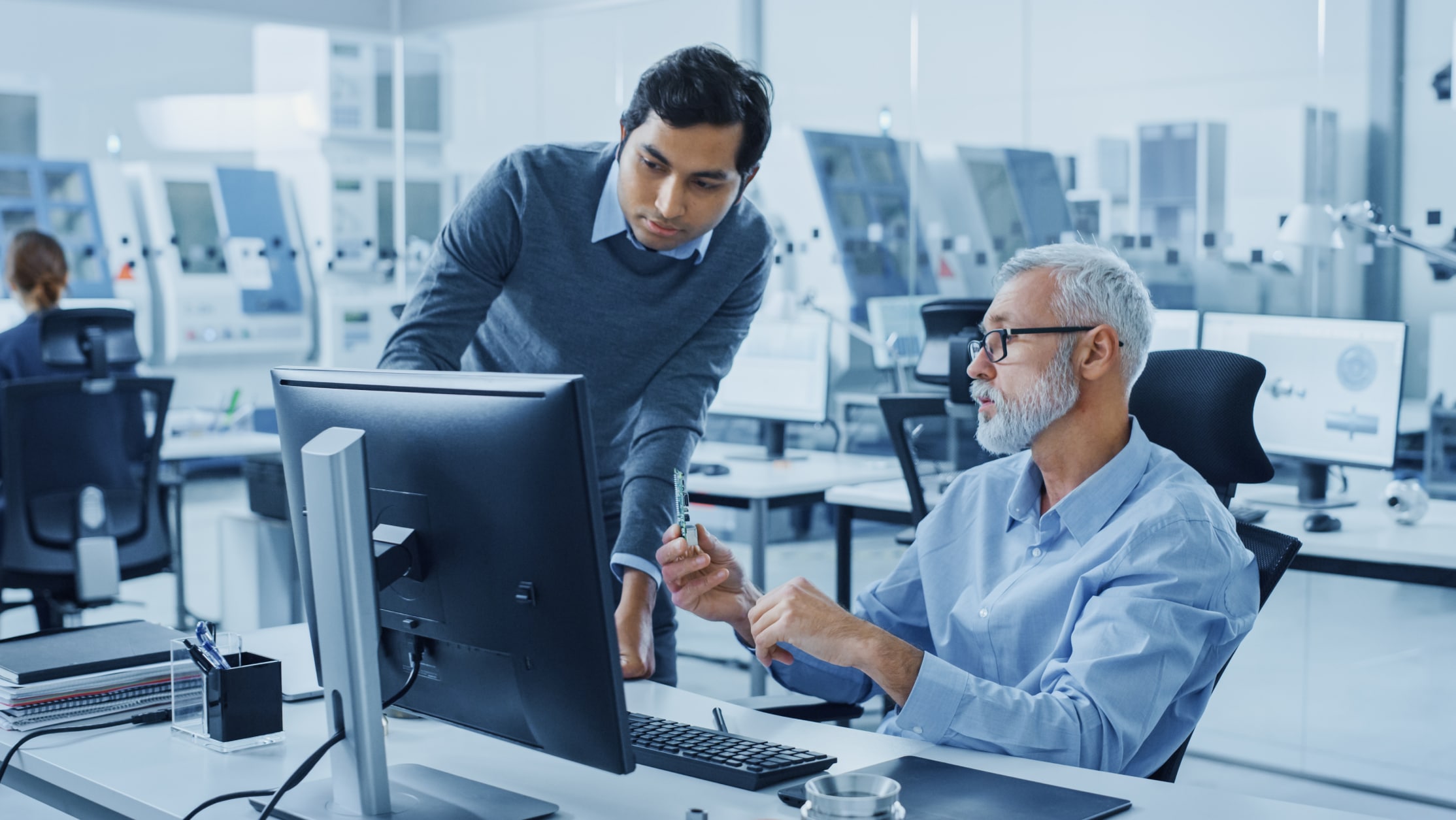
Discover the APS advantage for your linerless printers
By choosing APS linerless thermal printers, you’re investing in cutting-edge technology that enhances productivity, lowers costs, and supports a greener future. Contact us today to learn more about our linerless printing solutions and how they can transform your labeling process.