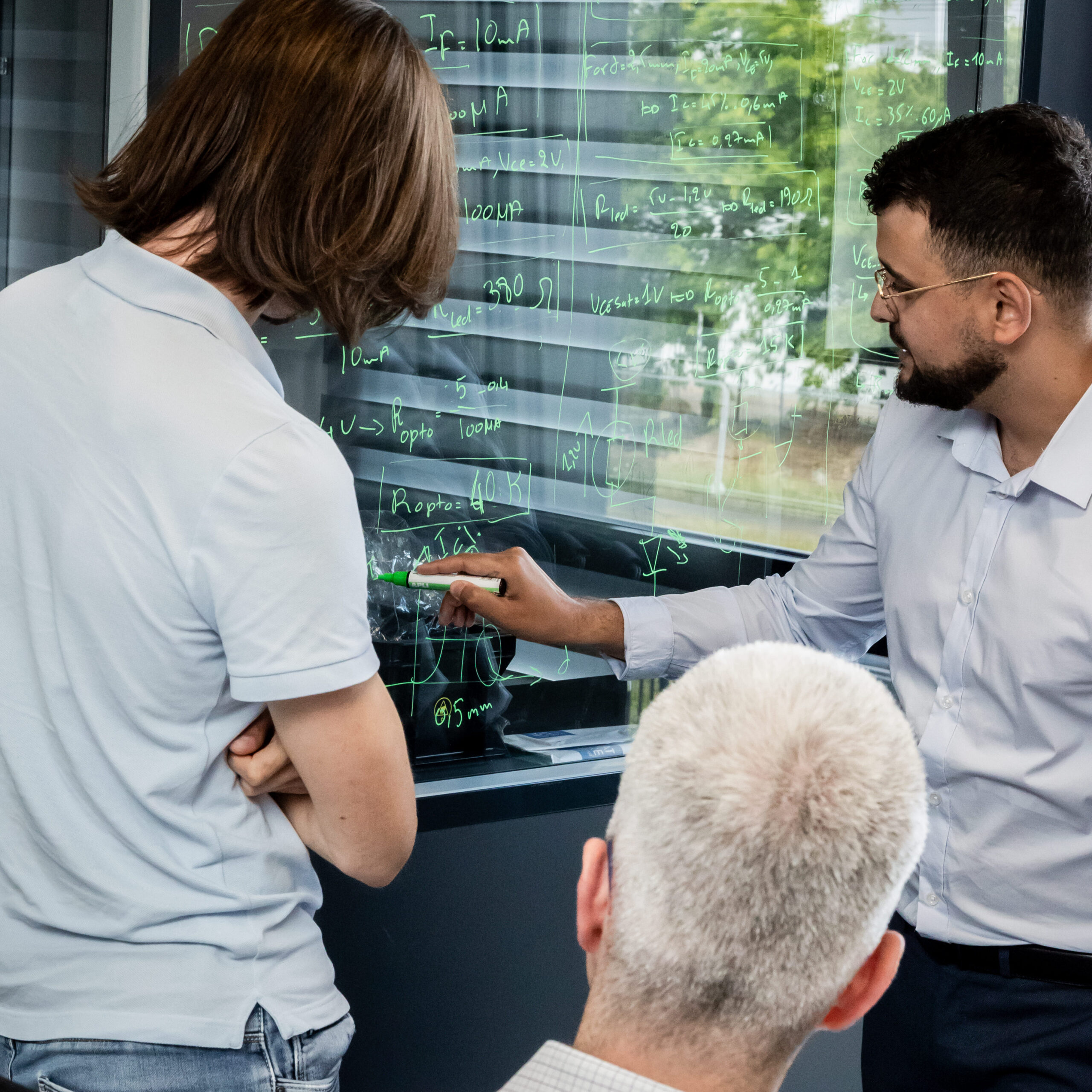
Thermal printers 101: understanding Direct Thermal vs. Thermal Transfer technology
Welcome to “Thermal printers 101”, a series of articles designed to help you understand the fundamentals of thermal printing technology. Whether you are new to this field or looking to refine your knowledge, this series will cover everything from how thermal printers work to their key components and best practices for optimizing performance.
In this first article, we’ll explore the two main types of thermal printing: direct thermal and thermal transfer. While both methods rely on heat to produce images, they differ significantly in terms of process, materials, durability, and ideal use cases. Understanding these differences is essential for selecting the right thermal printer for your business.
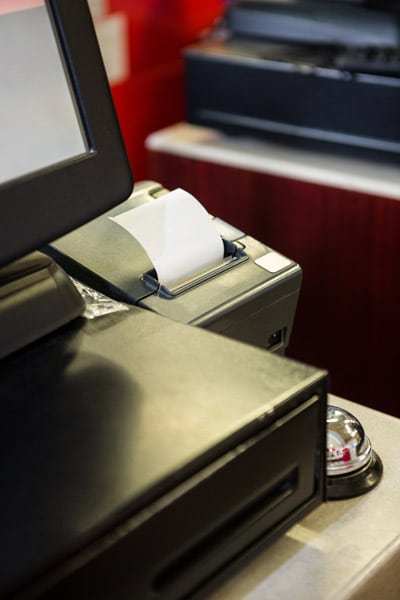
What is thermal printing?
Thermal printing is a digital printing process that uses heat to create an image on paper or another substrate. Unlike traditional printing methods that rely on ink or toner, thermal printers use specially coated materials that react to heat, making them ideal for high-speed and low-maintenance applications.
There are two main types of thermal printing:
- Direct Thermal printing
- Thermal Transfer printing
Each of these technologies has unique characteristics, making them suitable for different applications.
Direct thermal printing: how it works
Direct thermal printing uses heat-sensitive paper that darkens when exposed to heat from the printhead. The printhead selectively heats specific areas of the paper, producing an image without the need for ink, toner, or ribbons.
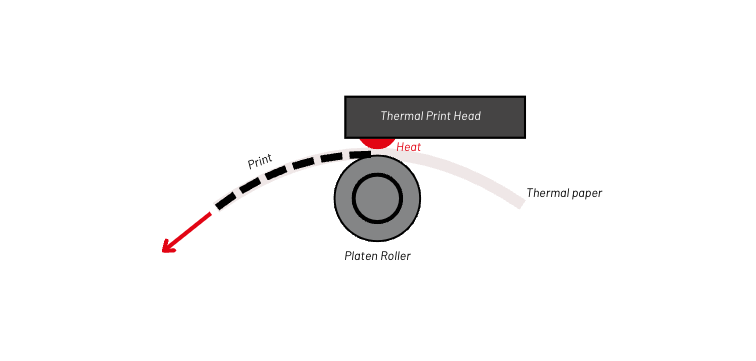
Advantages of direct thermal printing
✅ Cost-Effective: No need for ink, toner, or ribbons, reducing ongoing costs.
✅ Low Maintenance: Fewer moving parts mean less frequent repairs.
✅ Compact & Lightweight: Ideal for kiosk or handheld devices.
✅ Fast Printing: High-speed printing for receipts, tickets, and labels.
Limitations of direct thermal printing
❌ Shorter printout lifespan: Printed images fade over time, especially when exposed to heat, light, or chemicals.
❌ Limited Color Options: Only monochrome (usually black) printing is possible.
❌ Heat Sensitivity: The paper is susceptible to discoloration under high temperatures.
Best applications for direct thermal printing
Direct thermal printing is widely used for applications where short-term print durability is sufficient. Some common use cases include:
- Receipts & Tickets: Point-of-sale (POS) systems, parking tickets, airline boarding passes.
- Shipping & Logistics: Shipping labels, barcode labels, tracking tags.
- Medical & Healthcare: Patient wristbands, prescription labels.
Thermal transfer printing: how it works
Thermal transfer printing, on the other hand, uses a ribbon coated with ink (usually wax, resin, or a combination). The printhead applies heat to the ribbon, transferring the ink onto paper, plastic, or other materials.
This process creates high-quality, long-lasting prints that resist fading, heat, and chemical exposure.
Advantages of thermal transfer printing
✅ Durable & Long-Lasting: Prints do not fade over time.
✅ Versatile Material Compatibility: Works on paper, plastic, polyester, and other materials.
✅ High Print Quality: Crisp text and barcodes with excellent resolution.
✅ Multiple Color Options: Can print in different colors using specialized ribbons.
Limitations of thermal transfer printing
❌ Higher Cost: Requires ribbons, which add to operational expenses.
❌ More Maintenance: The ribbon mechanism requires occasional adjustments.
❌ Bulkier Design: Generally larger than direct thermal printers.
Best applications for thermal transfer printing
Thermal transfer printing is ideal for applications where long-term durability and high print quality are required. Some common examples include:
- Healthcare & Pharmaceuticals: Laboratory specimen labels, medical device tracking.
- Product Labeling: Barcode labels, retail tags, asset tracking labels.
- Industrial & Manufacturing: Chemical drum labels, circuit board labels, warehouse labeling.
Choosing between direct thermal and thermal transfer printing
Selecting the right thermal printing technology depends on factors such as durability, cost, and application requirements.
Durability and print longevity
Direct thermal printing is best for short-term applications, as the heat-sensitive paper can fade over time, especially when exposed to heat, light, or friction. This makes it ideal for receipts, shipping labels, and temporary identification tags. In contrast, thermal transfer printing produces highly durable prints that resist fading, moisture, and chemicals. This is why it is commonly used for product labeling, industrial barcodes, and asset tracking.
Cost considerations
If cost-efficiency is a priority, direct thermal printing has an advantage because it does not require ink or ribbons—only thermal paper. This reduces operating expenses and maintenance needs. However, thermal transfer printing, while involving higher costs due to ribbons, offers greater print longevity and can be more cost-effective for applications requiring long-lasting labels.
Print quality and material flexibility
Direct thermal printing provides sharp, high-contrast prints, but only in black and on heat-sensitive paper. On the other hand, thermal transfer technology allows for higher resolution, multiple colors, and printing on a variety of materials such as plastic, polyester, and synthetic labels.
Print quality and material flexibility
If you need fast, low-cost printing for short-term use, direct thermal is the way to go. If you require high-quality, long-lasting prints on different materials, thermal transfer is the better choice. Understanding these differences will help you make the right decision for your specific needs.
Why choose APS for your direct thermal printing needs?
At APS, we specialize exclusively in direct thermal printing solutions, offering high-speed, reliable, and cost-effective printers for industries that demand efficiency. Our technology eliminates the need for ribbons or ink, reducing maintenance and operational costs while ensuring consistent, high-quality prints.
With decades of expertise, APS designs compact, durable, and energy-efficient thermal printing mechanisms ideal for retail receipts, transportation tickets, medical labeling, and logistics tracking. Our innovative features, such as easy-loading mechanisms and long-life printheads, maximize uptime and ensure hassle-free printing.
If you need a robust direct thermal printing solution tailored to your industry’s needs, APS has the expertise and technology to support you. Contact us today to discover how our printers can optimize your operations!
Browse our thermal printer range
If you’re ready to embrace the future of thermal printing ? APS is here to help !
Contact APS today to learn more about our range of advanced thermal printers and how we can tailor solutions to meet the unique needs of your business.